Gauge Wheels: Planting’s season’s supporting act
If planting season was a rock concert, seed opener blades would be the stars of the show. But just as a rock star is nothing without the band, so seed opener blades rely on a supporting act – gauge wheels – to do their job.
The seed opener and the gauge wheel work in tandem to open a furrow at the correct depth, leaving enough soil in the right place for the closing wheel to place back over the seed. The specification of your gauge wheels will depend largely on which planter you’re running – but factors such as soil moisture, tillage system and even crop type can all inform your decision about which gauge wheel to choose.
Here’s a look at some of the options available on gauge wheels, and the factors to consider when making a choice.

Gauge wheel placement
The vast majority of planters have the gauge wheel positioned right next to the seed opener blade – and for good reason. This is the closest practical point to where the seed drops, and therefore the point at which you can achieve the most precise depth control, which has a direct impact on soil contact and seed germination.
Locating the gauge wheel alongside the blade also prevents soil from being thrown out of the furrow by the opener blades. This is important in no-till systems where minimal soil disturbance is the name of the game, and is also vital for successfully closing the furrow, since the close wheel can’t replace soil that is thrown too far from the furrow. It’s also important if your soil is prone to waterlogging, since moving too much soil out of the furrow can lead to depressions in the surface that collect water and can cause seeds to rot.
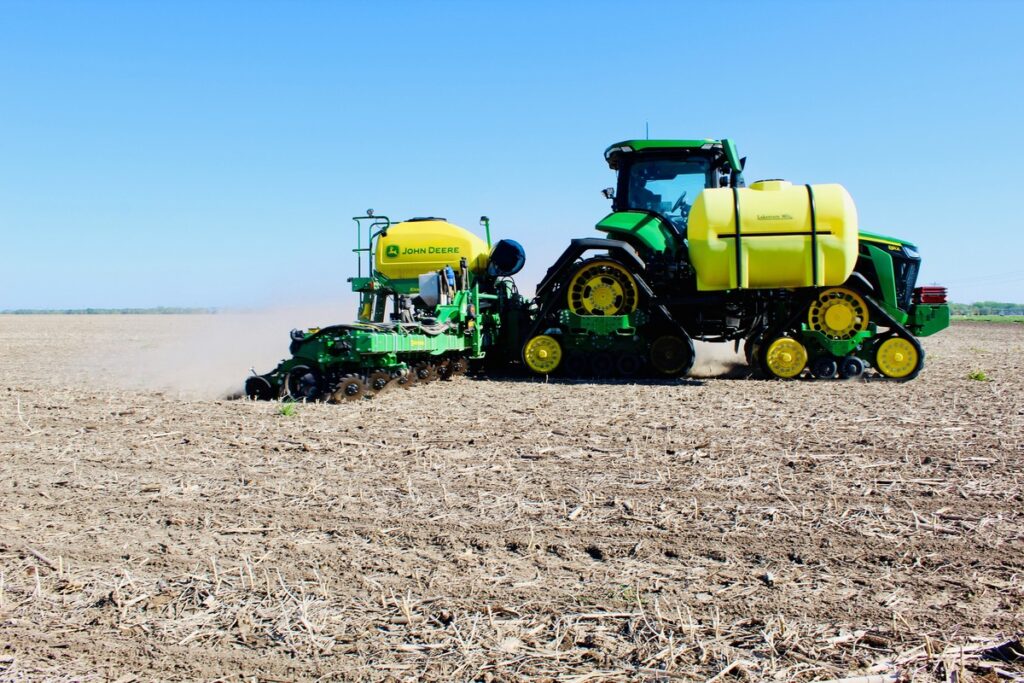
Soil compaction
The function of the gauge wheel is to hold down the sidewall of the furrow that naturally wants to rise up as the seed blade passes through. This results in a clean furrow that facilitates precise seed placement, and enough soil to effectively close it again. But an unwanted side effect of this is compaction of the sidewall, which can in itself cause problems with seed-to-soil contact, resulting in restricted root growth, poor emergence, and lost yield potential.
Some manufacturers – such as Case – have attempted to get around the problem with design tweaks to their machinery. The Case IH gauge wheel uses a Reduced Inner Diameter (RID) tire with a unique relief profile that leaves space for the soil to bulge upwards along the edge of the furrow, while still retaining a clean furrow profile. The system works thanks to a ‘seed boot’ that runs along inside the furrow itself, preventing the loose soil from collapsing inwards before the seed is placed.
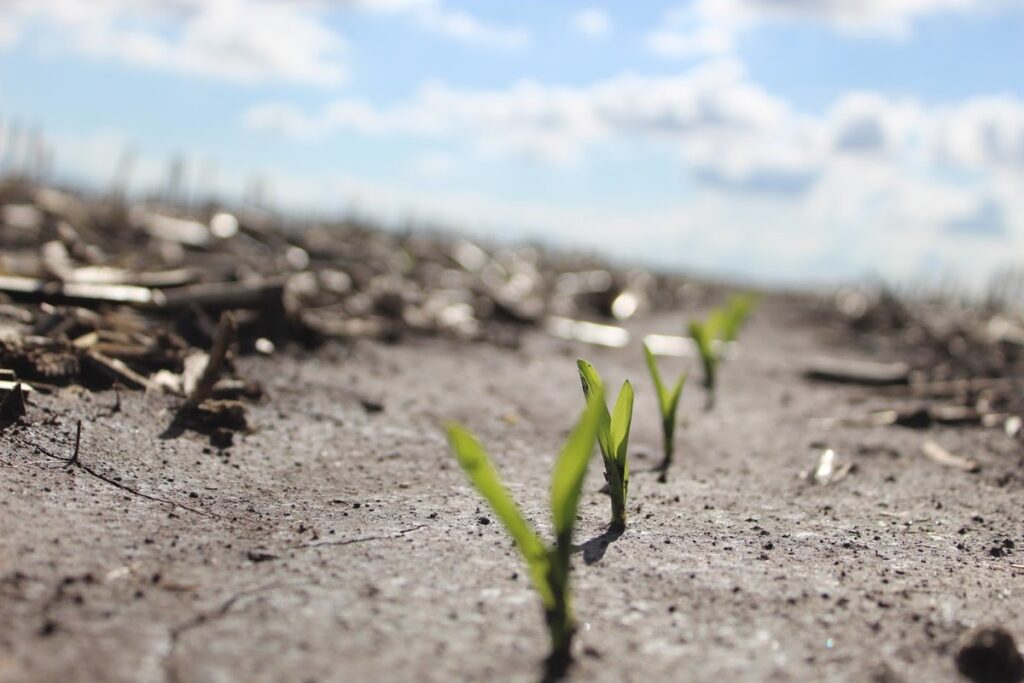
Choosing a width
Gauge wheels are available in a range of widths, typically 2.5”, 3” and 4.5”, with the latter being the most common. The width you choose depends on the importance of depth versus compaction – the narrower the wheel, the more depth you’ll achieve since the wheel is less prone to obstruction by trash or clumps of soil.
2.5-inch wheels are typically run on twin row planters because there isn’t room for a wider wheel. 3-inch wheels tend to be used in strip or ridge till systems, where they help to achieve a good balance between depth and soil compaction – but there’s an increasing movement towards their use in no-till systems too because of their ability to run smoothly through trash.
Gauge wheels over 4 inches in diameter are most commonly used in conventional tillage systems, but in no-till they’re an ideal choice on heavy soils where plugging is an issue. They serve to keep the row unit out of the ground and maintain consistent depth.
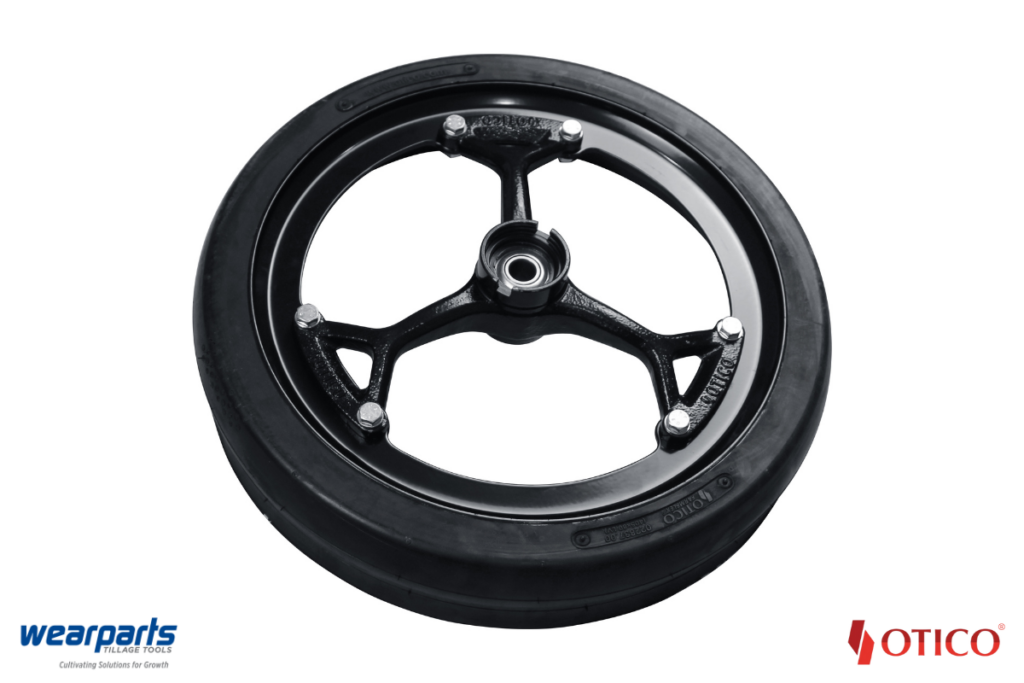
Spoked or solid?
Gauge wheels come in both solid and spoked profiles and the choice really comes down to soil conditions, farming system – and personal preference. The idea of spoked gauge wheels is that mud and residue can escape between the spokes so they don’t get clogged up, and also so that it’s easier to clean out any debris that gets lodged between the seed disc and the gauge wheel. However, in no till systems – particularly corn fields – the leftover corn stalks and other trash can end up getting tangled in the spokes, leading some farmers, especially those in drier climates, to opt for a solid wheel profile.
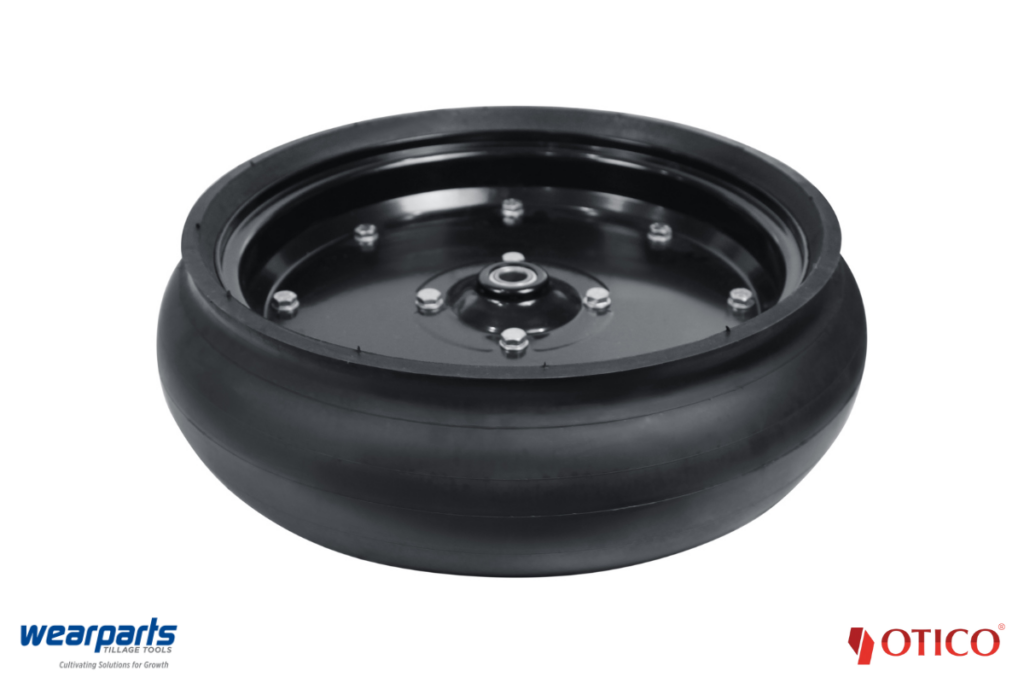
Which tires?
Gauge wheel tires always have a convex profile to reduce drag and therefore increase agronomic efficiency. They have traditionally been made of rubber, which has a key benefit – its flexibility allows the tire to easily shed mud and debris as it moves along.
But rubber tires struggle to stand up to the extreme wear they encounter in conservation tillage system – especially no-till, where corn stalks can shred up a tire like nobody’s business. For this reason, polyurethane tires are becoming more popular for gauge wheels. Polyurethane wheels retain their lips for much longer which results in a superior furrow – but they can also be heavy and hard, leading to increased soil compaction, and the risk of the tire bouncing over an uneven surface, leading to inconsistent depth. In addition, polyurethane wheels don’t shed mud easily so they are prone to plugging.
The solution? Rubber semi-hollow tires like the FarmFlex range by Otico, available from Wearparts. These tires are manufactured from rubber and are hollow like a normal tire, but the proportions have been altered to deliver superior performance. The void in the centre is just big enough to give the tire that necessary flex, while the rubber is thick enough to be puncture-proof and deliver that long-wearing, semi-rigid lip. Superior shock absorption ensure consistent planting and crucially, less wear and tear on your planter. Tire profiles vary by machine, and FarmFlex has options to fit them all – including the RID option for the Case IH planter.
For more advice on which gauge wheels are best for a specific planter or how you can tackle particular in-field challenges, contact our knowledgeable sales team.